How to Manage Warehouse Inventory? 4 Tips
Table of Contents
- Introduction
- A system to track inventory location
- Stack the items based on order frequency
- Periodical inventory audits
- Product labeling
It’s very common for companies to focus on warehouse management, while overlooking inventory management . The reason? Warehouse management and inventory management are deceptively similar. There’s a lot of overlap in warehouse and inventory controls, however the differences in inventory management controls are key, and not focusing on inventory management within a warehouse has major demerits. With poor inventory management, you can expect low visibility of stock, repeated cases of product loss and theft, and poor fulfillment records.With poor inventory planning within the warehouse, floor workers get frustrated in identifying the products quickly, impacting the delivery process.
Managing inventory within the warehouse is all about receiving, tracking, auditing, and fulfillment of the orders—it covers a sequence of crucial steps. Fulfillment takes a hit in the absence of proper inventory management.
Here are our top 4 tips
With all that in mind, how do you manage warehouse inventory?
1. A centralized system to track inventory location
Determining where the inventory is stored in simple steps is crucial to a fast and efficient warehouse operation. You can have serial tracking, lot tracking, or a combination of both to make the job of warehouse operators easy. This will reduce the time taken to pick, pack and ship.
Suppose you are a business that deals with high-value utility but sells in low quantities. In that case, serial tracking helps, whereas lot tracking would be the best fit for business models with low-value utility and high quantities.
Tracking as a process will reduce the instance of overselling or stock-out, especially when the sale is facilitated through omnichannel commerce. Having an inventory management system is the foremost requirement when we talk about the ways and means on how to control inventory in a warehouse. Such a system will manage the inventory in real-time, update stock levels independently, and automate the mundane tasks in the fulfillment process.
2. Stack the items based on order frequency
Arrange the most popular or best-selling items in the racks close to the packing area. Likewise, identify the revenue generated by products and determine their position in the warehouse. For example, the revenue and profit margin from Fitbit watches are higher when compared to any other product. They consume less space in a warehouse setup. Therefore, they can be parked in an area close to the packing space.
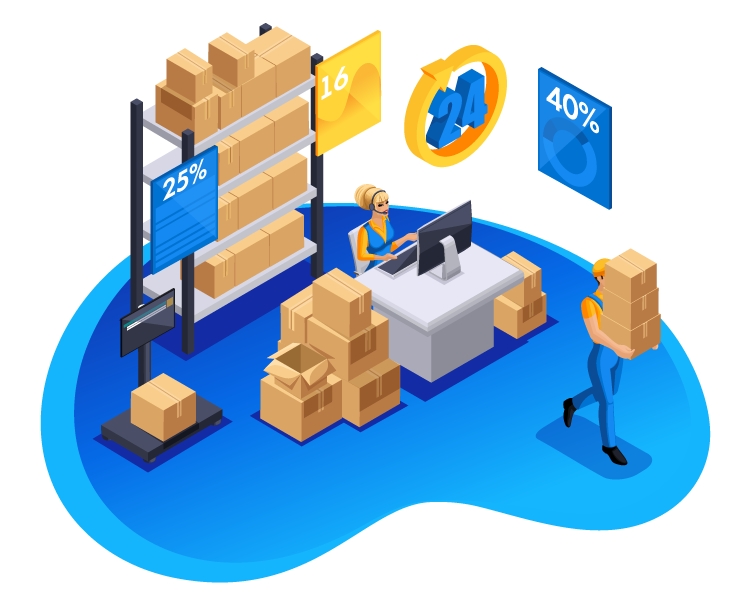
3. Conduct periodical inventory audits
Inventory control is the second-most dessential process on the topic of how to manage warehouse inventory. The objective of inventory control is to audit the number of units of goods stored in the warehouse to prevent theft or loss. Often, if theft or loss occurs, the warehouse manager is unaware until someone on the floor informs them specifically. Therefore, a regular cycle count—quarterly or yearly— will help you keep a check on the inventory. Of course, this ,is notwithstanding the surprises inventory audit can bring to the surface — theft of an entire lot, or some units of stock, etc. And all these are very possible over the course of time. It’s best to keep a tight control and crack the whip regular inventory cycle counts.
4. Prioritize product labelling
When you label your products, pickers find it easy to spot the right inventory without confusion. The faster the picking and packing process, the higher the warehouse efficiency rate. Fool-proof labeling of products has many long-term benefits:— minimizes the time spent in identifying the inventory, cuts down labor costs, fewer instances of lost orders, and much more. Given the fast-paced buying habits of customers, warehouses have to adapt and to accommodate growing demands by simplifying and organizing their operations.
When you label your products, pickers find it easy to spot the right inventory without confusion. The faster the picking and packing process, the higher the warehouse efficiency rate. Fool-proof labeling of products has many long-term benefits:— minimizes the time spent in identifying the inventory, cuts down labor costs, fewer instances of lost orders, and much more. Given the fast-paced buying habits of customers, warehouses have to adapt and to accommodate growing demands by simplifying and organizing their operations.
Recent Blog Posts
Inventory management is an essential aspect of any business that deals with physical products. Efficient inventory management can help a company reduce costs, improve customer satisfaction, and increase profits.
Warehouse management refers to the processes and systems involved in managing a warehouse's operations, including receiving and storing goods,
December is challenging for organizations—not to achieve peak productivity levels but to maintain the least status quo in productivity. The reason is the flurry of activities that are taking place this month.
Warehouse management and inventory management have a significant impact on companies' profits, as well as on their smooth, efficient and proper operation.
The bread and bakery industry has been experiencing steady growth due to the rise in
Companies within the food and beverage distribution industry face stiff competition. These companies strive
5% to 10% of the average annual budget of the fleet goes in vain.