Top 10 common inventory issues and how to fix them?
Inventory management is an essential aspect of any business dealing with physical products. Having a well-efficient inventory process in place can help companies reduce costs, improve customer satisfaction, and increase profits. However, several common inventory management challenges are faced by businesses. Here are the top 10 that they encounter:
Overstocking or Understocking:
One of the most common challenges is overstocking or understocking. Overstocking can lead to excess inventory, higher carrying costs, and potential obsolescence. Understocking can lead to lost sales and dissatisfied customers.
Solution: Businesses can prevent overstocking by accurately forecasting demand, tracking inventory levels in real-time, and using automated reorder points. Understocking can be avoided by setting safety stock levels, having alternative suppliers, and utilizing just-in-time inventory systems.
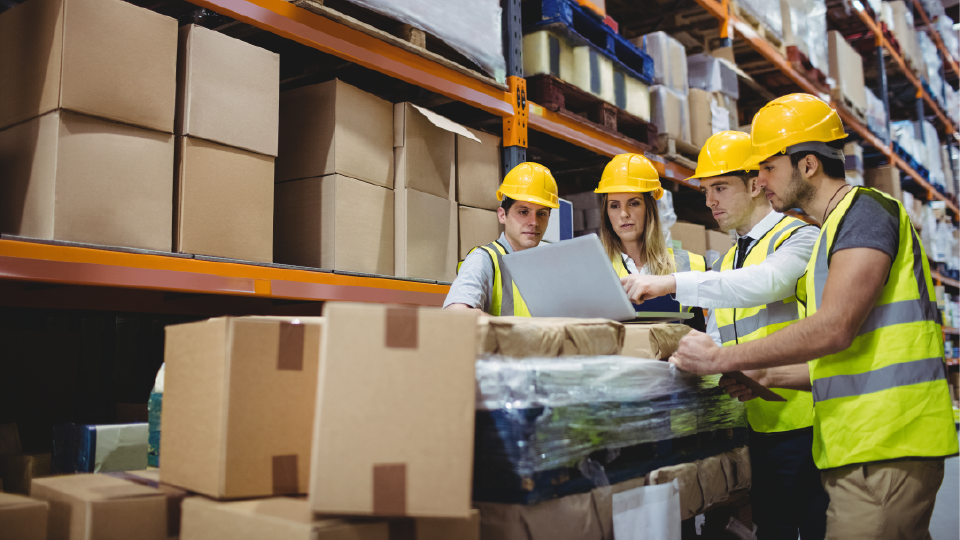
Poor inventory tracking
If a business does not have a proper inventory tracking system in place, it can lead to inaccurate inventory counts, misplaced items, and difficulty fulfilling customer orders.
Solution: Adopting an inventory system that includes barcoding, RFID tagging, or other tracking technologies can help improve inventory accuracy and reduce the likelihood of misplaced or lost items.
Inefficient processes
Manual inventory processes can be time-consuming and prone to human error. This can result in inefficient operations and delayed order fulfillment.
Solution: Implementing automation tools such as automated reorder points, barcode scanners, or inventory management software can help streamline inventory management processes, increase accuracy, and reduce manual labor.
Lack of coordination between departments
Lack of communication and coordination between different departments can lead to poor inventory practices and inefficient operations.
Solution: Implementing regular communication and collaboration between departments such as sales, purchasing, and operations can help improve inventory management practices and increase efficiency.
Inaccurate demand forecasting:
Inaccurate demand forecasting can lead to overstocking or understocking, which can result in lost sales, excess inventory, or obsolescence.
Solution: Businesses can improve demand forecasting accuracy by analyzing historical sales data, market trends, and customer behavior. Using automated demand forecasting software can also help businesses accurately predict future demand.
Poor supplier management:
Poor supplier management can result in delayed deliveries, poor quality products, and increased costs.
Solution: Businesses can improve supplier management by establishing strong supplier relationships, setting performance expectations, and monitoring supplier performance regularly.
Lack of Automation:
Manual inventory processes can be time-consuming and prone to errors, leading to inefficiencies and inaccurate inventory tracking.
Solution: Implement an inventory solution that automates inventory tracking and management processes. Automation can help improve accuracy, reduce the risk of human error, and save time.
Inefficient Warehouse Layout:
An inefficient warehouse layout can lead to lost time, lost productivity, and increased labor costs.
Solution: Optimize your warehouse layout to minimize the distance that inventory needs to be moved, reduce congestion, and improve accessibility. Use technology such as warehouse management systems to help manage inventory more efficiently.
Lack of real-time visibility:
Lack of real-time visibility can make it difficult for businesses to make informed decisions about inventory planning.
Solution: Implement a modern inventory system that provides real-time visibility into inventory levels, sales data, and other key metrics. This can help businesses make data-driven decisions and respond quickly to changes in demand.
Inefficient inventory handling:
Inefficient inventory handling can lead to damaged or lost products, which can result in higher costs and lower customer satisfaction.
Solution: Use tested and proven handling processes, such as first-in-first-out (FIFO) or last-in-first-out (LIFO), to ensure that products are handled properly. Proper training for employees can also help improve handling efficiency.
Tackling these challenges must be the foremost priority of any business that strives to achieve on-time order fulfilment and improve customer satisfaction.
Recent Blog Posts
Inventory management is an essential aspect of any business that deals with physical products.
Inventory management is an essential aspect of any business that deals with physical products. Efficient inventory management can help a company reduce costs, improve customer satisfaction, and increase profits.
Warehouse management refers to the processes and systems involved in managing a warehouse's operations, including receiving and storing goods,
December is challenging for organizations—not to achieve peak productivity levels but to maintain the least status quo in productivity. The reason is the flurry of activities that are taking place this month.
Warehouse management and inventory management have a significant impact on companies' profits, as well as on their smooth, efficient and proper operation.
The bread and bakery industry has been experiencing steady growth due to the rise in
Companies within the food and beverage distribution industry face stiff competition. These companies strive
5% to 10% of the average annual budget of the fleet goes in vain.